Stöckli is one of Switzerland’s oldest ski manufacturers. swissinfo.ch / Dominique Soguel-dit-Picard Shortages of raw materials and logistics bottlenecks have made 2021 a tough year for Swiss manufacturers, and contributed to a downgrade in the government’s GDP growth forecast for the economy next year. Swissinfo.ch’s India specialist covers a wide range of issues from bilateral relations to Bollywood. He also knows a thing or two about Swiss watchmaking and is partial to the French-speaking part of Switzerland. More from this author | English Department The secret ingredient that’s helped earn Switzerland’s Stöckli its reputation as one of the best ski brands in the world is a special glue made of raw materials imported from England and Japan. So crucial
Topics:
Swissinfo considers the following as important: 3.) Swissinfo Business and Economy, 3) Swiss Markets and News, Business, Featured, newsletter
This could be interesting, too:
Nachrichten Ticker - www.finanzen.ch writes Die Performance der Kryptowährungen in KW 9: Das hat sich bei Bitcoin, Ether & Co. getan
Nachrichten Ticker - www.finanzen.ch writes Wer verbirgt sich hinter der Ethereum-Technologie?
Martin Hartmann writes Eine Analyse nach den Lehren von Milton Friedman
Marc Chandler writes March 2025 Monthly
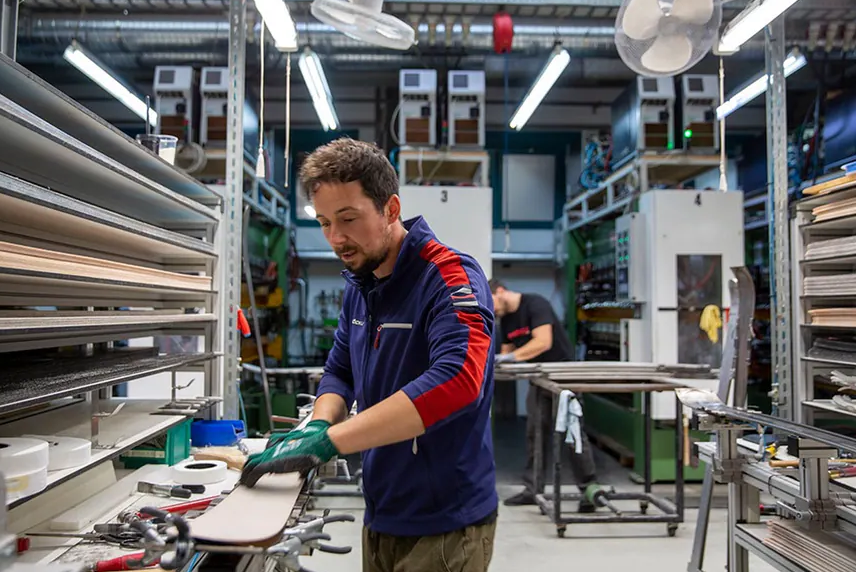
Stöckli is one of Switzerland’s oldest ski manufacturers. swissinfo.ch / Dominique Soguel-dit-Picard
Shortages of raw materials and logistics bottlenecks have made 2021 a tough year for Swiss manufacturers, and contributed to a downgrade in the government’s GDP growth forecast for the economy next year.
The secret ingredient that’s helped earn Switzerland’s Stöckli its reputation as one of the best ski brands in the world is a special glue made of raw materials imported from England and Japan.
So crucial is the Japanese powder to the production process that the award-winning company has always ensured it has enough inventory to weather virtually any storm. So when the double whammy of the coronavirus pandemic and the global supply chain crisis hit, it was well prepared.
What the Swiss company did not foresee, however, was having to scramble to get all the other raw materials that go into making a pair of skis – from the wooden cores to the steel used in the tips. “We thought it was going to be a sprint but it was a marathon,” says Christoph Fuchs, chief manufacturing officer at Stöckli Swiss Sports AG, which has been making skis since 1935 and counts rising star Marco Odermatt, currently leading the men’s 2021 Alpine Skiing World Cup, as a customer. “Each time we solved one challenge, the next one came and then the next.”
Stöckli is one of hundreds of Swiss manufacturers affected by the global supply chain disruption triggered by the coronavirus pandemic and the blocking of the Suez Canal in March by the Ever Given container ship. The toll on the economy was laid bare on December 9, when the Swiss government cut its forecast for growth in 2022 to 3% from 3.4%. The State Secretariat for Economic Affairs (SECO) blamed the downgrade on uncertainty surrounding the Covid-19 pandemic and “international supply and capacity bottlenecks” that are putting pressure on industry and causing sharp price increases globally. The government also raised its forecast for consumer inflation next year to 1.1% from 0.8% because of increased prices for energy and materials.
“A slowdown in the economic recovery would also be likely if the global capacity bottlenecks were to last longer than expected and inflation increases were to lead to sustained price pressure with significantly higher interest rates,” the SECO said in a statement.
Companies must invest
With experts predicting supply chain problems will persist well into 2022 and possibly 2023, companies are now having to focus on risk mitigation, to identify and manage their vulnerabilities.
“Not only has Covid got politicians talking about supply chains, it has also shown companies that they need to take supply chain management seriously,” says Stephan Wagner, a supply chain specialist at the Swiss Federal Institute of Technology in Zurich (ETHZ). “Companies have to be willing to invest in something that is unlikely to happen”.
For Stöckli, the supply problems started in the spring with a three-week holdup in deliveries of plastic to its factory in the central canton of Lucerne, some 60 kilometres southwest of Zurich. The delays soon spread to other materials. Woods like Paulownia, a light, warp-resistant hardwood grown mostly in east Asia, arrived several weeks late in the summer because suppliers in Austria were affected by shipping bottlenecks in China. Adhesives, rubber, and metals also took two to three times longer to arrive. The company was forced to switch its production schedule for nearly 30 models of skis and change materials and even suppliers in some cases.
“The goal was to keep production running,” says Fuchs. That required constant planning and communication with 25 suppliers as well as tweaking production processes so that skis could be assembled as soon as all parts became available. The delivery time for wood orders increased to eight or 10 weeks from five, he notes. The biggest headache in the autumn proved to be aluminium, a lightweight metal that is added as a layer to the wood core of the ski to add strength. It now takes 24 weeks to arrive from Austria, instead of eight. Stöckli was lucky to have enough in stock to tide it over until new supplies arrived. Even so, the delays meant employees were required to work night shifts and weekends to make sure the company was ready for the start of the winter skiing season in December.
Getting hold of raw materials has not been the only challenge. Prices of raw materials used in Stöckli skis have risen on average by 10% this year, according to Fuchs. The highest increase — 20% — was for the signature adhesive in its skis. “We are a small player in the ski industry and if we want to get the materials on time we could only say yes to the higher prices,” says Fuchs. That is a cost the company — rather than consumers — will have to absorb this winter season because the increases hadn’t kicked in when prices with retailers and distributors were fixed in the first quarter of 2021.
Global bottlenecks
So what is causing the supply chain problems afflicting the world? Christoph Wolleb, director of supply chain management and operations at KPMG Switzerland, identifies three main factors: shortages of key raw materials, logistics issues including a lack of ships and containers, and factory closures in Asia caused by Covid-related restrictions.
“Closing a factory for a week does not just mean companies have to wait a week longer for products,” he says. “The whole supply chain gets thrown into disorder and recovery takes 10 times longer than the disruption.”
Like most of Europe, Switzerland is still reeling from the effects of pandemic-related port closures across the globe, as countries imposed lockdowns to stop the spread of the virus. Docks in the Asia-Pacific region and the US continue to deal with backlogs and congestion, which has led to a global shortage of shipping containers and made it more difficult and expensive to transport goods by sea from Asia to Europe.
“Even before Covid, the demand for logistics resources was high but Covid led to a global overheating of the logistics industry,” says Wolleb. “It is now 10-20 times more expensive to ship a container from Shanghai to Basel.” According to logistics firm Freightos, one can expect to pay $14,381 to ship a container from Asia to northern Europe, an increase of 538% compared to the same time last year.
The consequences are reverberating across the Swiss economy, not only at manufacturers like Stöckli, but also in the retail sector. A search on the Bike World website in the first week of December illustrates the problem. A men’s mountain bike model (Ghost Kato Essential, CHF599) is available to order online but a racing bike model (Liv Avail Advanced 1, CHF3,199) has only two units left. A lady’s bike model (Diamond Topaz Villiger, CHF1,099) can only be delivered in four weeks and a children’s bike model (Scott Scale 24, CHF499) in 15 weeks.
Not all shortages are related to the pandemic, says Wolleb, pointing to timber, which is used in construction. “Demand was high even before Covid and when Covid hit there was panic buying similar to what happened with toilet paper,” he says. “Wood parasites in eastern and central Europe and uptick in US orders made it worse.”
Biggest challenge
Supply chain disruption is now the biggest challenge facing small companies in Switzerland, according to the Economic Barometer published by Swissmechanic, an industry association for small and medium-sized enterprises in the machinery, electronic and metal sectors. In a survey published in the third quarter of the year, some 54% of respondents from 174 firms listed supply chain issues as the biggest challenge they were facing, well ahead of other concerns such as labour shortages and a lack of orders.
Swiss suppliers of components to the global auto manufacturing industry are being affected by disruptions to vehicle production caused by semiconductor shortages and other supply chain bottlenecks. Autoneum Holding AG makes parts for acoustic and heat protection systems and has factories in 55 locations around the world including China and South Korea.
“Autoneum is indirectly affected by the current market development as a result of the chip shortage and other bottlenecks in the supply chain of vehicle manufacturers,” Claudia Güntert, head of corporate communications for the Winterthur-based manufacturer told swissinfo.ch in an email.
Its plants have had to adjust production to cope with the changing output schedules of its customers and as a result the company has laid off temporary staff and implemented short-time working, Güntert said. But the company expects the situation will start to improve in 2022, based on strong demand from consumers, and sees output returning to pre-Covid levels in 2023 as pent-up customer demand held back by the semiconductor shortage is unleashed, she said.
Feintool International Holding AG, a Swiss manufacturer of engine and transmission components for the automotive industry, has cut production of high-volume parts as a result of supply chain bottlenecks at its customers, Karin Labhart, a spokeswoman for the company, said in an email.
“Call-offs from customers have become extremely short-term due to the chip and steel shortage,” Labhart said. “We try to react flexibly to customer requirements, which makes predictability very difficult compared to the first half of 2021.”
Shortages of steel as well as semiconductors are causing problems in Feintool’s own supply chain and has required the company to change the way the business is run, including planning with both customers and suppliers on a weekly and even daily basis, Labhart said. Production, logistics and working hours have all had to become more flexible to meet customer requirements, she said.
Even ABB, one of Switzerland’s biggest companies that manufactures heavy-duty power equipment, has been affected. Speaking on its third-quarter earnings conference call in October, CEO Björn Rosengren said the biggest pain point for the company has been procurement of semiconductors. “The supply chain bottlenecks will be with us for several more quarters,” said Rosengren, as reported by the agency AWP.
Rethinking the supply chain
Faced with the prospect of continued shortages for months if not years, companies need to rethink how they manage their supply chains, says Wagner, the supply chain expert from ETHZ. They could start by investing in dual sourcing, using more than one supplier for a given raw material or component, to ensure that a minimum level of inventories can be maintained. Firms also need to identify their indirect suppliers and eliminate risk factors, for example by avoiding dealing with companies in the same location, he said.
The last time companies seriously reassessed supply chain risks was after the 9-11 terrorist attacks in the US, Wagner says. They spent two to three years building resilience and identifying weak links to protect themselves in the event of further incidents, but let these plans lapse after attacks failed to materialise. “Supply chain risk management involves costs, and it does not make money if nothing bad happens,” he says.
The reluctance to invest in making supply chains more resilient was aggravated by the global financial crisis of 2008. Many suppliers went bankrupt after orders were cancelled and the experience made those who survived wary of investing in spare capacity, says Wolleb of KPMG. Companies chose outsourcing and offshoring instead of investing in alternative suppliers and giving themselves more time to fulfil orders.
“As in manufacturing, supply chains have been optimised and made lean over the last few decades to offer just-in-time delivery and cut costs,” he says. “The global supply chain is overheated and we have made it even worse by introducing additional pressure points like Black Friday.”
Is reshoring the answer?
Wolleb says the time has come to talk seriously about bringing manufacturing back to Europe. He points to recent trends in the textile industry, one of the first to move manufacturing to Asia. Many companies are now bringing production closer to home, to eastern Europe and even western Europe. This option has become increasingly viable as greater use of automation has cut the need for labour and as rising wages in Asia have weakened its competitive advantage. The development of customer centricity – such as personalisation of products – will also be easier to achieve with reshoring, says Wolleb.
Wagner from ETHZ agrees that there is a shift toward producing critical items closer to end markets and says that companies will be more selective about offshoring production in sectors that can be automated and do not need cheap labour. However, he is not totally convinced.
“We cannot reverse globalization,” he says. We rely on certain competencies in certain parts of the world. At the end of the day, are consumers willing to pay twice as much for a car?”
Covid wild card
Despite the challenges thrown up by the pandemic and supply chain disruptions, fans of Stöckli, including Odermatt, who will be heading to the Winter Olympics in Beijing in February, will still be able to get their hands on a pair of skis.
Fuchs is confident that the company has done enough to mitigate its supply chain risks. Orders are being placed with suppliers well in advance, the shelves at the Stöckli warehouse are stocked and machines buzz as workers grind and polish skis into shape. In a best-case scenario, production could return to pre-Covid levels of around 60,000 pairs of skis per year from about 40,000 this year.
But with Covid cases rising again across the world, and the new Omicron strain threatening to trigger renewed lockdowns, the pandemic is, once again, the biggest threat.
“We would have to think really hard about how we are going to survive that,” says Fuchs.
Tags: Business,Featured,newsletter